Fusion energy may be the holy grail of clean energy, but harnessing its complex processes and machinery is a daunting task. Researchers at DIFFER think the solution to fusion may not only lie in deeper physics understanding but also in an engineering approach to self-steering systems.
In the final months of 2023, researchers and engineers from across Europe are in a race for fusion on the Culham Science Campus near Oxford. Their Joint European Torus (JET) reactor has been Europe’s flagship experimental fusion device for forty years and will enter retirement and decommissioning in the new year. A last experimental campaign squeezes every last bit of scientific insight from the doughnut-shaped fusion device.
As a last hurrah, the JET team even manages to set a new world record for the most fusion energy released in a single shot – an important step towards harnessing the power of the Sun as a clean energy source on Earth. But this experimental campaign is about much more than records.
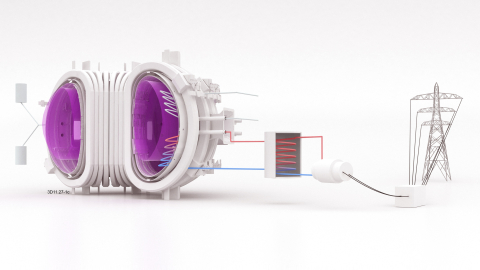
Heat exhaust
Part of JET’s last experiments are three carefully tailored ‘shots’ – ten-second bursts of 100 million degrees Celsius – that have nothing to do with pushing the reactor to maximum output, and everything to do with managing the heat exhaust in future fusion power plants.
Running the three shots is a team of Dutch researchers, among whom is PhD candidate Thomas Bosman. A control engineer from the Dutch Institute for Fusion Research, Bosman, has been given temporary control over a humble gas valve at the inside bottom of JET. Its crucial role: to puff in enough gas to cool and diffuse the hot exhaust near JET’s inner wall, without adding so much gas that it snuffs out the core of the plasma (hot, charged fuel particles) where fusion reactions take place.
Bosman explains: “In JET, the plasmas are short and relatively benign. Sturdy wall materials like tungsten can manage the heat directly.” Future fusion power plants will be an order of magnitude more powerful, with much harsher conditions. He continues: “If you do not manage the heat exhaust very carefully, you could damage the inside walls in seconds.”
Engineering approach
Physicists call the regime where heat is diffused before it touches the reactor wall ‘detachment.’ They have spent years understanding the underlying interactions between the outer plasma edge, the plasma core and the reactor walls. Bosman and his colleagues instead managed to fine-tune a control algorithm that guarantees detachment in just three ten-second plasma shots, without knowing any of the underlying physics: a great success for the engineering approach to fusion.
In his PhD work at DIFFER, Bosman uses the insight that while the underlying physics of the fusion exhaust may be complex, the way the entire system behaves in response to a puff of cold gas can be caught in a basic model. Bosman recalls: “During those shots in JET, we studied how the exhaust responds to slow and fast changes in the amount of cooling gas that we puffed in. In principle, that was all the information we needed to set the rules for our controller.”
Confidence
Bosman and his colleagues in the DIFFER team on control engineering did not just swoop in and solve a grand challenge in fusion research in half a day. Getting there took years of physics research to understand the heat problem and develop a scenario to manage it; without that solid foundation, Bosman’s controller would not know where to start or what to achieve.
After successful first steps in exhaust control on the small Swiss fusion experiment TCV in 2021, the team was invited to do the same for the larger German fusion experiment ASDEX-Upgrade. Only then did the fusion community have enough confidence in the new technique to green-light dedicated experiments at JET in the UK, where experimental time is a scarce resource.
Even after this success, Bosman thinks detachment remains a challenge. He says: “The optimal fusion performance is close to the upper limit where your gas puffing starts to impact the plasma core. But once we switch on our system, our controller can maintain the exhaust in exactly the desired state.”
Full scenarios
Important as the heat exhaust may be, in the grand scheme of control engineering, it is a fairly simple system. A so-called linear equation suffices to model the response of the exhaust to outside stimuli like puffs of gas. But fusion knows many more complex, non-linear challenges, like how to foresee and manage growing instabilities, like sudden lightning-like energy outbursts from the edge of the fusion plasma. And what about long-term issues like the slow erosion of a reactor wall over months of operation?
One of the leaders in DIFFER’s fusion research is plasma physicist and computer modeller Sven Wiesen, an expert in understanding the many interacting processes that happen at the edge of a fusion reactor.
Take the case of ITER, the world’s largest fusion experiment to date. Wiesen says: “You do not just want to model the very edge of your plasma; what happens there is ultimately decided by processes upstream in the heart of the plasma.” That includes the effect of fusion heat generated in the plasma core, the magnetic cage keeping the hot mass of charged particles in place, and the turbulence that transports heat outward to the scrape-off layer, the point where plasma leaves the magnetic cage and flows towards the exhaust area.
All these processes influence each other in highly non-linear behaviour. Preparations for the ITER design were done in computer models like the Scrape-Off Layer Plasma Simulator (SOLPS). Wiesen explains: “When the ITER design was finished in the 90s and 2000s, SOLPS was the tool to create complete exhaust scenarios for how to operate it.”
Bells and whistles
From the level of turbulence and energy outbursts from the plasma edge to their effect on the fusion reactor wall, SOLPS can model it all. At a price, says Wiesen: “With the full bells and whistles of including every last process, each scenario took months to calculate on a supercomputer.” Over the years, Wiesen has learned that those high-fidelity models are crucial for the field. He says, “Simplified codes don’t cut it. If you make approximations or leave out processes, you just don’t get the right answers.”
While high-fidelity models have their place in giving fully detailed operating scenarios, the increased pace in the fusion community demands faster, more agile predictions. Wiesen is part of a movement that uses machine learning and artificial intelligence to train so-called surrogate models. Those identify trends in the output of more detailed models and can reproduce the same overall behaviour in minutes instead of months. Or faster, shares the physicist: “With the new AI methods, we are now at the point where we can predict future behaviour faster than the plasma itself evolves.”
While surrogate models only work with confidence if they can interpolate between solid data points, they open up new possibilities in the world of fusion. Control engineer Thomas Bosman: “An advanced controller could have a fast model of the plasma inside to look ahead at what the plasma will do. That would let it look predictive if, for instance, there is unwanted behaviour coming up, and decide how to tweak conditions now to dampen or avoid those conditions.”
Private parties
Asked about the applications of surrogate models, Wiesen names interested parties like the US privately funded SPARC project and the British public-private project STEP. Interestingly, both feature different configurations from existing reactors like JET. For instance, SPARC operates at a much higher magnetic field strength compared to ITER and STEP’s plasma is shaped more like a cored apple than the doughnut shapes found in other reactors. Wiesen: “For all those differences, the underlying physics is basically the same. With a proper scaling, if it exists, that lets us port our predictions without problems.”
Even ITER has shown interest, shares the physicist: “To get the go-ahead for their first shots from the licensing agency, they need to prove that it will go through in advance.”Which is tricky, because there is no similar experiment they can pull experimental data from; ITER is twice the size of its direct predecessor, JET. But fast models could extrapolate the performance of previous devices to the ITER parameters in a trustworthy way, thinks Wiesen. “That would show the necessary confidence in their approach.”
Network approach
Do fusion control algorithms always have to lean on physical understanding? Coming into the field from a PhD in system theory, DIFFER post-doc researcher Lizan Kivits has a surprising take on this. Within this topic, network identification is a very new field, with its first scientific publication in 2013. And it may herald a revolution in our understanding of highly connected networks of components.
Essentially, the field of systems theory is a highly mathematical field. Network theory can be used to describe any network, from the thousands of components on a modern computer chip to the millions of parts inside a fusion reactor. Its approach is to focus on interconnected subsystems within a network, where both the behaviour of subsystems and their interconnections are taken into account.
Kivits says: “When my colleagues talk about the physics of plasmas, I find it hard to follow them.” But as soon as she has measurements of physical quantities, Kivits can identify the dynamic interactions between them from experimental data. She says, “For instance, how the heat in the core of the plasma influences the number of plasma particles at the edge.” All without using a single physics formula.
Both DIFFER’s engineers and physicists agree that fusion physics and control theory have a lot to offer each other. Thomas Bosman says: “In the academic community, we develop very advanced, smart control algorithms, but real-world industrial applications mostly use quite simple, linear control schemes. Fusion may be one of the few fields where we actually need to implement these advanced control algorithms. And in return, those controllers offer a unique way to bring fusion energy closer to reality.”
This article appeared on the Innovation News Network website and will also appear in the 23rd edition of the platform's quarterly publication.
Author: Gieljan de Vries
Go to the News page.