A heat shield of liquid metal automatically limits the temperature of a fusion reactor's inner wall, no matter how high the incoming heat load. PhD candidate Peter Rindt (TU/e and DIFFER) tested 3D-printed prototype holders for liquid metal in DIFFER's research facility Magnum-PSI and discovered that a protective vapor shield above the liquid metal self-regulates the surface temperature to 800-900 oC. Self-repairing and self-protecting liquid walls are an attractive concept for future fusion power plants, where the reactor walls need to withstand extreme temperatures and particle impacts for months to years between repairs. Peter Rindt and colleagues published their tests of liquid-metal infused prototypes in Nuclear Fusion, the leading scientific journal in this field.
Vapor shielding and self-repairing walls
Heat shields in fusion reactors (divertors) are exposed to extremely concentrated heat loads around 10 MW/m2, and intense particle impacts. These components must survive for two years under perhaps the harshest conditions that any man made object must live through: comparable to conditions at the surface of the sun or a rocket exhaust. The solution may lie in protecting the divertor with a thin layer of liquid metal which can repair itself by flowing in new liquid after being damaged. Moreover, evaporated liquid forms a vapor shield in front of the divertor which can diffuse power to other parts of the reactor before it reaches the divertor.
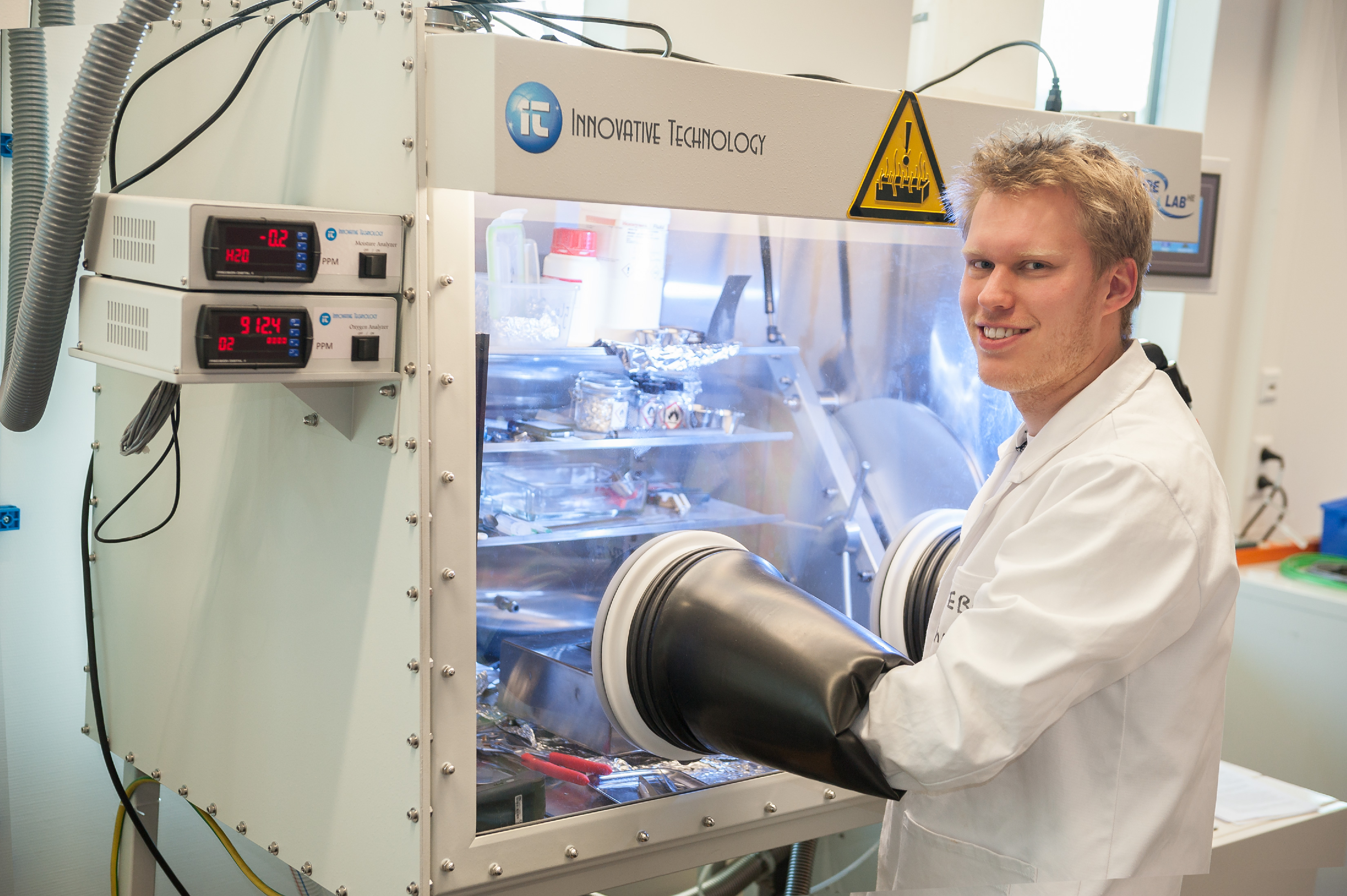
Future fusion power plants
Fusion researchers want to mimic the process that powers the sun and stars as a clean, safe and abundant power source on earth. By forcing hydrogen isotopes together at extreme temperatures, they fuse together to form helium and release tremendous amounts of energy which can be harvested. To build fusion plants capable of 24/7 operation, it is crucial to design a reactor that can stand up to these punishing conditions.
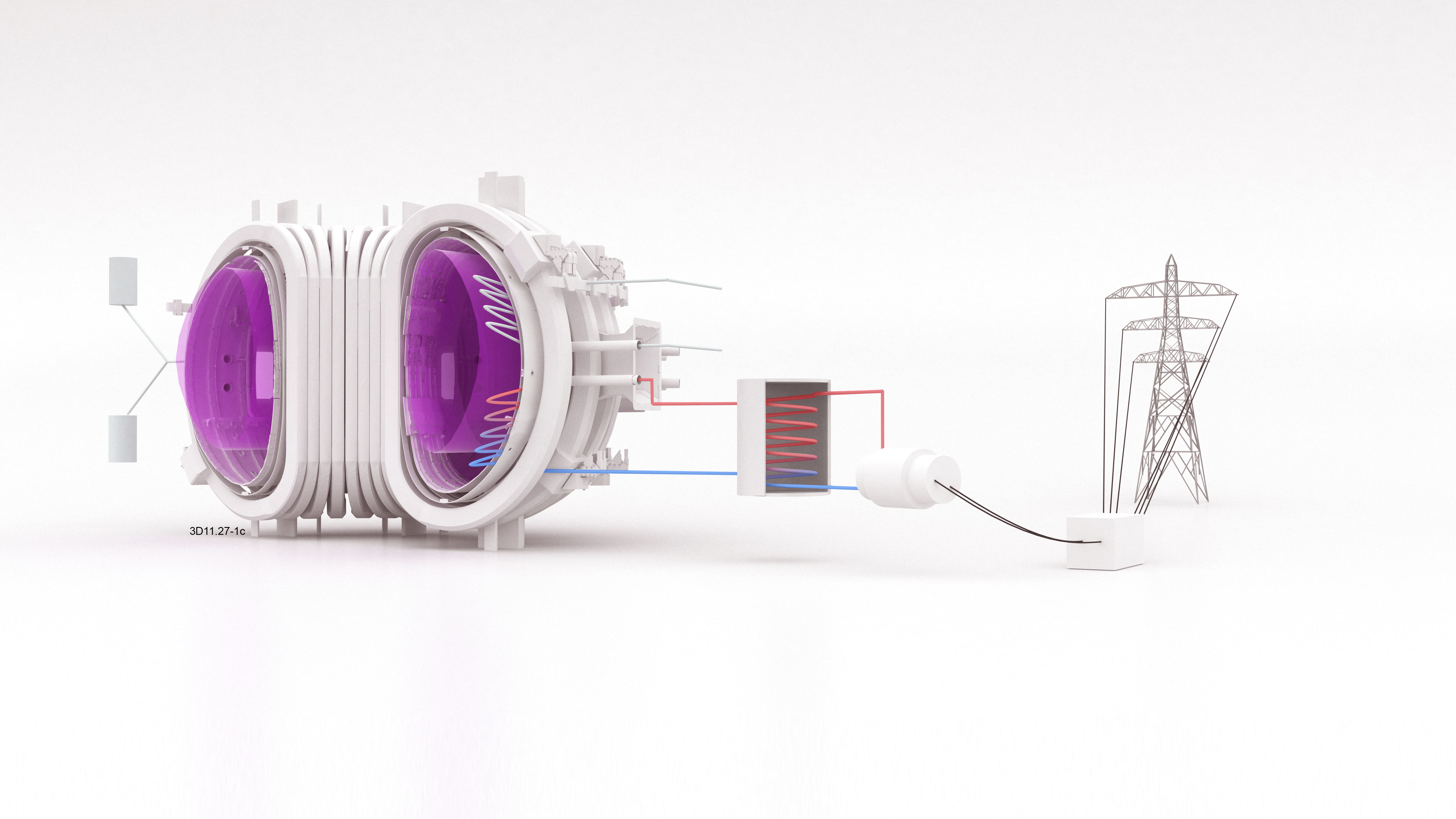
Realistic tests
Peter Rindt and his team tested the workings and limitations of vapor shielding by soaking lithium in a tungsten sponge and exposing their two prototype designs to reactor-grade plasma conditions in DIFFER's facility Magnum-PSI. This device is the only laboratory facility in the world capable of producing the extreme heat loads and particle bombardment in a fusion reactor. Peter Rindt: "We saw that the surface of the lithium-filled sponge barely increased past 800-900 ̊C, no matter how high the incoming heat load was. A model we had run earlier had predicted this as the temperature where evaporation becomes strong enough to form a vapor shield. This was the first demonstration of this effect in steady state operation."
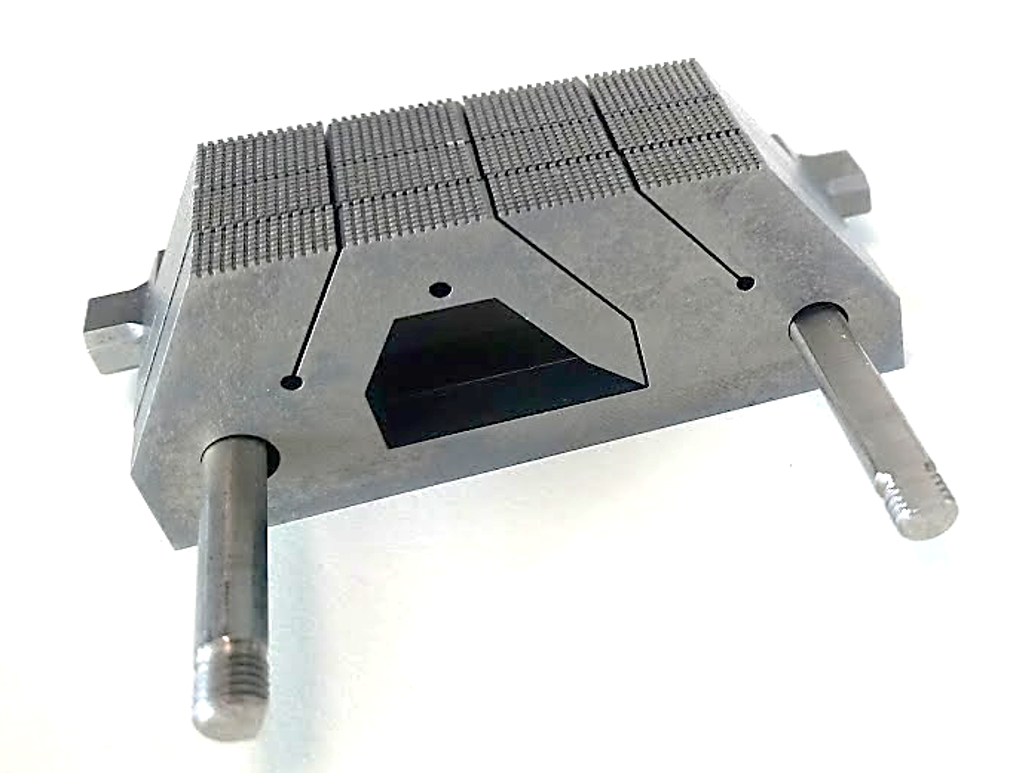
The "sponge" used in this research is nothing ordinary. Rindt's team tested a new concept which works like an oil lamp: the surface where the power from the plasma hits has a spongy texture, but underneath it is connected via thin channels to a larger reservoir. This extra liquid metal supply allows the concept to be used in experimental fusion reactors without constant refilling. Two prototype generations were tested, the second of which was made via 3D-tungsten printing in collaboration with Dunlee. These prototypes have vastly increased flow to replenish the surface, to make sure it never dries out. Using a smart geometry made it possible to avoid any material stresses due to heating and expansion. "This is highly promising", thinks Peter Rindt: "in a fusion reactor material properties degrade faster than anywhere else, due to the high number of particle impacts by fast particles from the fusion plasma. A design which can withstand those conditions is good news for fusion."
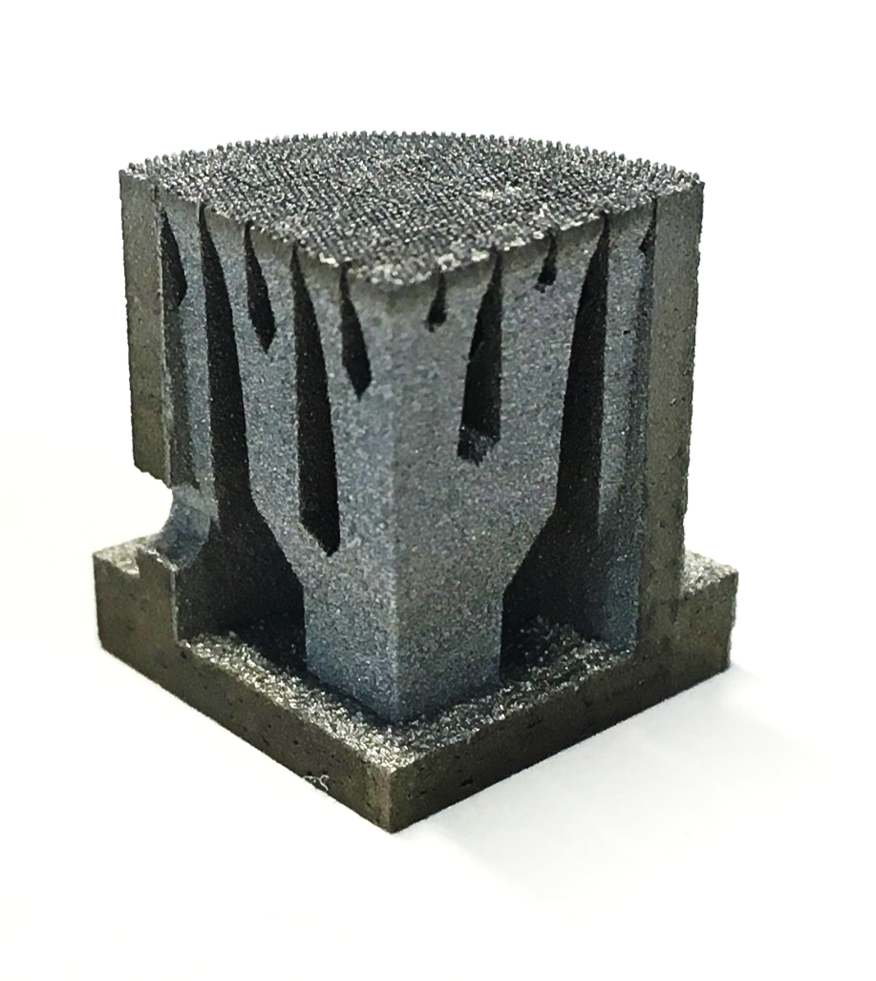
Read the original publications:
Go to the News page.