Future fusion power plants require a careful balancing act to protect their insides from the hot plasma exhaust. DIFFER control engineer Thomas Bosman designed and tuned a control algorithm for this thorny problem in only three experimental shots. On 30 April 2025, he successfully defended his PhD thesis at Eindhoven University of Technology.
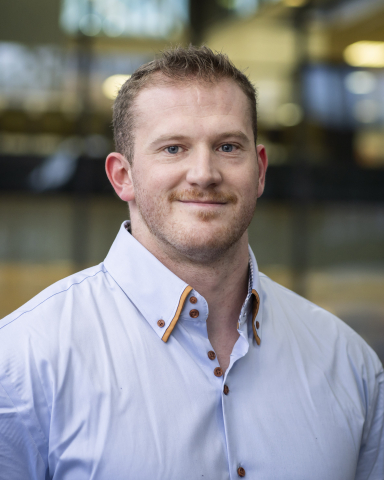
Controlling the hot exhaust of fusion reactors is a complicated problem. A 100-million-degree artificial star blazes in the plasma core, which needs to vent its reaction product to the inside walls of the reactor. Even cooling down to some 20,000 degrees Celsius on the way outward, the heat load is too high for any material to handle.
Fusion researchers want to manage the exhaust by puffing cooling gas into the exhaust stream before it hits the wall. But how do you do that without accidentally extinguishing the plasma core? For a physicist, understanding the detailed behaviour of the particles in the plasma core, edge and exhaust is key. But as an engineer trained in control theory, Thomas Bosman knows the value of taking a different view.
Systems approach
In his PhD work at DIFFER, Bosman used the insight that while the underlying physics of the fusion exhaust may be complex, the way the entire system behaves in response to cooling gascan be caught in a basic model.
Bosman's challenge then became to put numbers to the speed and magnitude of how the hot plasma responds to a puff of cooling gas. Plug those numbers into a governing algorithm, and you can let this controller keep the exhaust gas at a level that is manageable for the wall without impacting the plasma core; no need to understand the movement of every individual atom in the process.
Live experiments
After PhD predecessors at DIFFER proved the technique at the smaller Swiss fusion experiment TCV, Bosman was allowed to apply their approach on the larger machines ASDEX-U in Germany and JET in the UK.
"It took only three shots to identify how the exhaust responds to slow and fast changes in the stream of cooling gas", says Bosman: "Those got us all the information we needed to define our controller."
With this controlling algorithm, research goals were achieved for which a 1.5-year research program was planned originally. "It is still tricky work, because ideal performance is close to the upper limit where you start to impact the plasma core. But once we switch on our system, our controller can keep the exhaust in exactly the desired state."
Private companies
Bosman was even able to apply his control scheme during the record-setting DTE3 campaign at JET in 2023, proving that this control scheme works under realistic conditions and with the same fuel mix as will be used in future fusion power plants.
Asked where he will go next: "This is a really interesting time for fusion, with a lot of progress at private companies. I will stay at DIFFER for now as a postdoc researcher, working on heat-exhaust control for the private fusion company CFS in Boston. And after that, who knows?"
PhD Thesis
Density profile and heat-exhaust control in nuclear fusion devices: Development of control methods in view of the operation of fusion power plants
Thomas Bosman, Energy Systems & Control group DIFFER
Go to the News page.