The worldwide production of synthetic hydrocarbons relies heavily on the Fischer-Tropsch process, but the basic steps in the formation of the carbon chains remain elusive. Scientists working at Syngaschem and DIFFER used advanced spectroscopic studies to understand what happens at the surface of the catalyst. They present their results in Nature Communications.
When, in the early 1920s, German chemists Franz Fischer and Hans Tropsch developed a process that could turn carbon monoxide and hydrogen into liquid hydrocarbons, they might have expected their invention to become relevant to the production of synthetic fuels. They were right. The Fischer-Tropsch process has become the cornerstone of the gas-to-liquid (GTL) and coal-to-liquid (CTL) industries that produce large volumes of synthetic fuels from natural gas or coal. But they probably did not foresee that it would take another hundred years to get a glimpse of what is actually happening at the heart of the process: the formation of carbon-carbon bonds that enable the production of long carbon chains. "This really is a very fundamental issue", says Kees-Jan Weststrate, senior scientist at Syngaschem B.V., a research company based at DIFFER. "Even though Fischer-Tropsch synthesis is so widely used, a thorough understanding is still lacking."
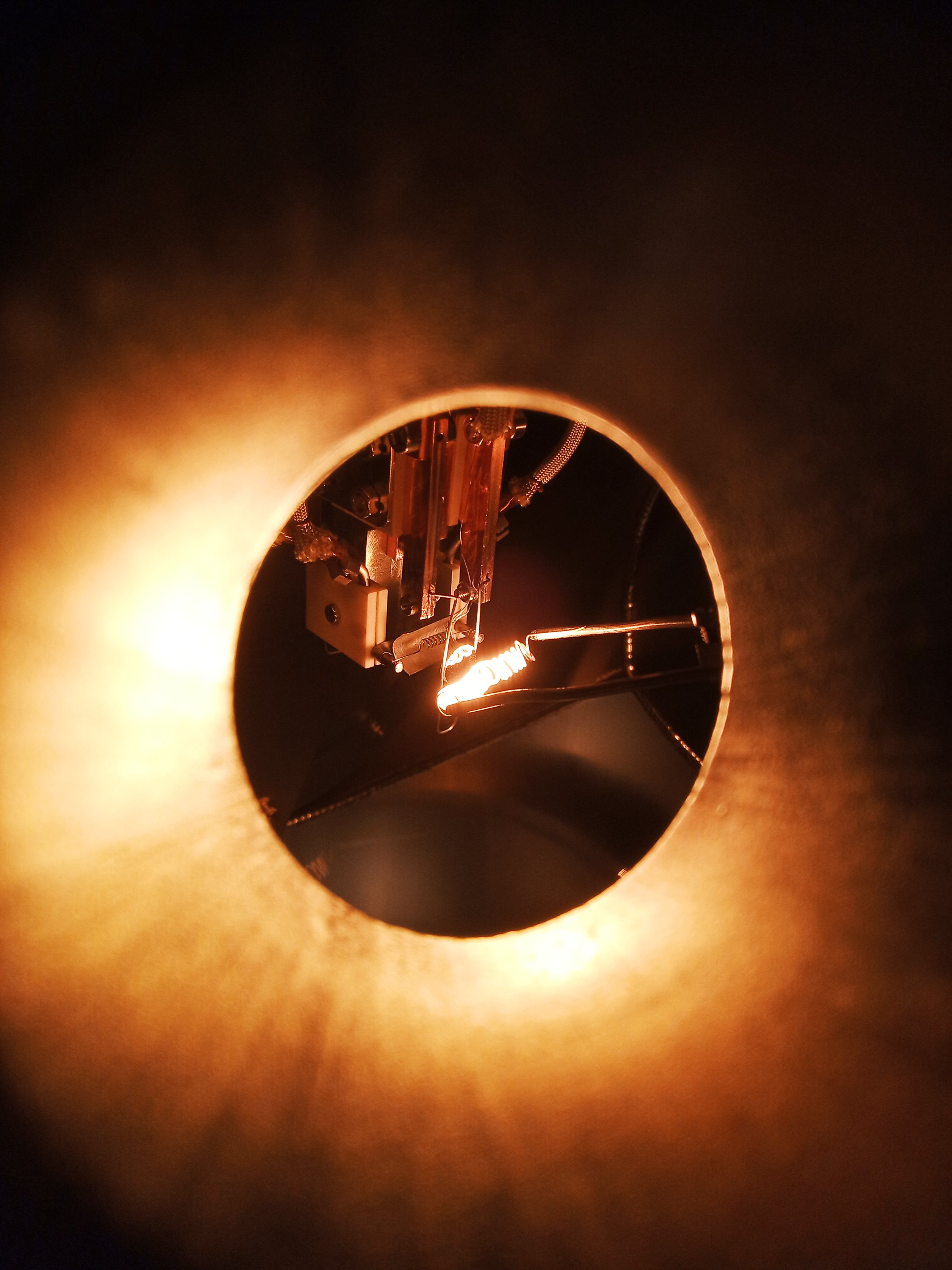
catalyst,a small disc of cobalt metal, is being heated.
The feedstock for Fischer-Tropsch synthesis is so-called synthesis gas or 'syngas', a mixture of carbon monoxide (CO) and hydrogen (H2). Heating up this mixture in the presence of a metal catalyst (mostly cobalt, iron or ruthenium) initiates the reaction between the two gases that leads to a collection of hydrocarbons of various lengths. "So far, most attention has been paid to the splitting of the C-O bond leading to a reactive carbon species, because that step is often seen as the rate-determining step of the whole process", Weststrate explains. "The second step, the formation of the carbon chains, has been taken for granted. You just create a mixture of hydrocarbons that will undergo a refinery process similar to crude oil."
Creating a more selective and efficient process, in which only hydrocarbons of the desired length are produced, requires a deeper understanding of what really happens at the surface of the catalyst. "Splitting of the C-O bond is important as it produces the reactive carbon species needed to grow the long chains. But the addition of carbon to the growing chain only takes place at the catalyst surface. The efficiency of carbon-carbon bond formation during that time determines the nature of the final product. As soon as the chain leaves the surface, the reactions stop and there will be no further growth. "
Too messy
One of the reasons that we know so little about these basic steps lies in experimental difficulties. Weststrate: "The main problem is that the real-life process is too complex and too messy to study in detail." That is why the team opted for an extremely simplified system. "We used a cobalt crystal with only one facet and as a building block we limited ourselves to ethene, a small molecule that contains only two carbon atoms and four hydrogen atoms, C2H4. Our aim was to elucidate the role of CO in the formation of carbon-carbon bonds and to determine what the ideal intermediate carbon species is for further chain growth."
The experiment started by binding ethene to the cobalt surface at very low temperature, to ensure that the molecules initially remain intact. Next, the temperature was slightly increased, leading to decomposition of ethene into acetylene (C2H2) and two hydrogen atoms which also adsorb to the surface. The temperature is decreased again to keep everything adsorbed, CO is added followed by very gradual heating. And then, everything changes, according to Weststrate. "The presence of CO has a huge effect on the process. Once CO adsorbs to the surface, the acetylene turns into an ethylidyne and switches to a 'standing' position. One of the carbons remains adsorbed, whereas the other comes free and sticks out, perpendicular to the catalyst surface. This position turns out to be the intermediate that can grow and our experiments showed that two ethylidynes dimerize to form 2-butyne, a chain of four carbon atoms."
Synchrotrons
Put like this, it sounds all very straightforward, but it involved a series of very advanced experimental set-ups that required specialized facilities, including two synchrotrons. At the SuperESCA beamline of ELETTRA in Trieste, the measurements at very low temperatures were performed. "That allowed us to really separate the various reaction steps. By working under vacuum, very gradually increasing the temperature and using the highly defined radiation from the synchrotron, we could determine the exact order of the reactions steps."
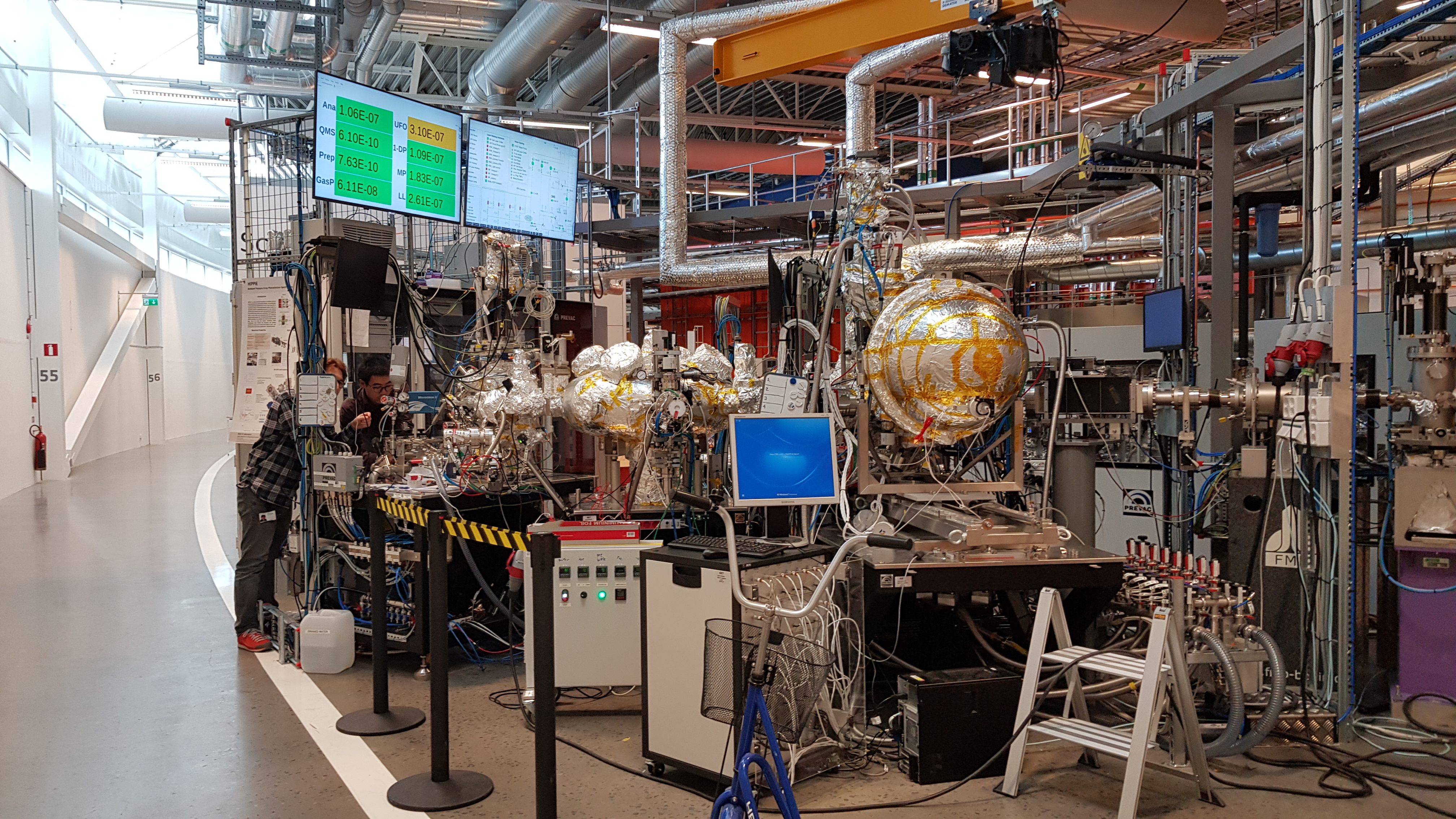
while exposing the sample to reactive gasesto mimic the reaction conditions used in industry.
Next, the team visited the HIPPIE beamline of MAX IV in Lund. "Here, we could work under much higher pressures and this time, we kept the temperature constant so we could watch what happens over time. We found that just adding more hydrogen to fill up the surface had no influence on the adsorbed acetylene. But then, surprisingly, CO showed up, probably due to a contamination. And again, that's when things started to happen. Acetylene turned into ethylidyne, switched up and dimerized to form 2-butyne. Taken together, our results led us to the conclusion that CO acts as stimulating spectator. As soon as CO gets adsorbed to the catalyst, everything is set in motion."
The big question is of course how these insights from a model system can be translated to the complex reality of the industrial Fischer-Tropsch process? Can we derive generic principles from this? Weststrate remains modest and cautious. "We know from other experiments that when you start with propene, which contains three carbon atoms, the process runs in a similar way, including dimerization to hexyne, leading to a six-carbon species. But when it comes real-life Fischer-Tropsch synthesis, the gap is still too wide. We can only draw conclusions on what we have actually measured, but what we can say is that both the presence of CO and the level of crowdedness on the catalyst surface play an important role. Our work can help the current thinking on how a catalyst actually works."
Text: Esther Thole
More information
Mechanistic insight into carbon-carbon bond formation on cobalt under simulated Fischer-Tropsch synthesis conditions, C. J. (Kees-Jan) Weststrate, Devyani Sharma, Daniel Garcia Rodriguez, Michael A. Gleeson, Hans O. A. Fredriksson & J. W. (Hans) Niemantsverdriet, Nature Communications, 6 February 2020
News release by the MAX IV Synchotron: The role of synthesis gas in tomorrow’s sustainable fuels
Go to the News page.